Overview
Business Modernisation for Support (BMfS) is a Ministry of Defence programme designed to enhance the delivery of frontline support. I was part of the team tasked with this initiative, starting in the alpha phase with a focus on gathering user insights and testing assumptions. Our goal was to identify key opportunities to carry forward into the beta phase.
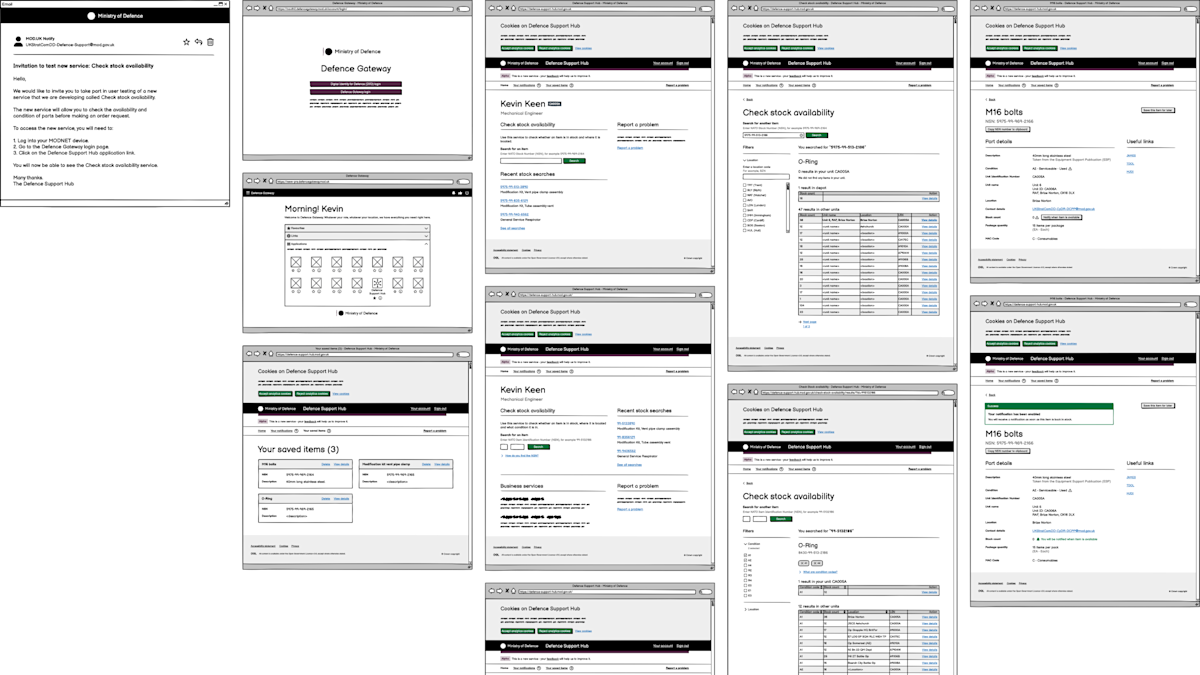
Opportunities
We identified and explored four key opportunities, focusing primarily on Engineers, with Logisticians as our secondary user group. Our efforts were directed towards gaining a deeper understanding of their needs and the context in which they order parts. The opportunities consisted of:
- Find Equipment Support Publication (ESP)
- Find NATO Stock Number
- Check Stock Availability
- Check Demand Status
User personas
We developed three distinct personas that, while fictional, provided realistic representations of our target users. We frequently referenced these memorable persona names to guide our design decisions.
Fig. 1 - Junior army mechanical engineer Fig. 2 - Army engineer Fig. 3 - Logistician
Prototype testing
We tested our ideas for all four opportunities by showing prototypes to users. This helped us better understand their needs, challenges, and how each idea could benefit them. All four opportunities had the potential to meet user needs, either on their own or when combined. However, we did face some technical difficulties in making them work.
For example, services like Check Stock Availability and Check Demand Status rely on having access to inventory data. If we could access this data through APIs or other methods, these features could be successfully implemented.
Low-fidelity paper prototypes for Check Stock Availability
We designed an end-to-end user journey for the Check Stock Availability, allowing users to search for items using a NATO Stock Number (NSN).
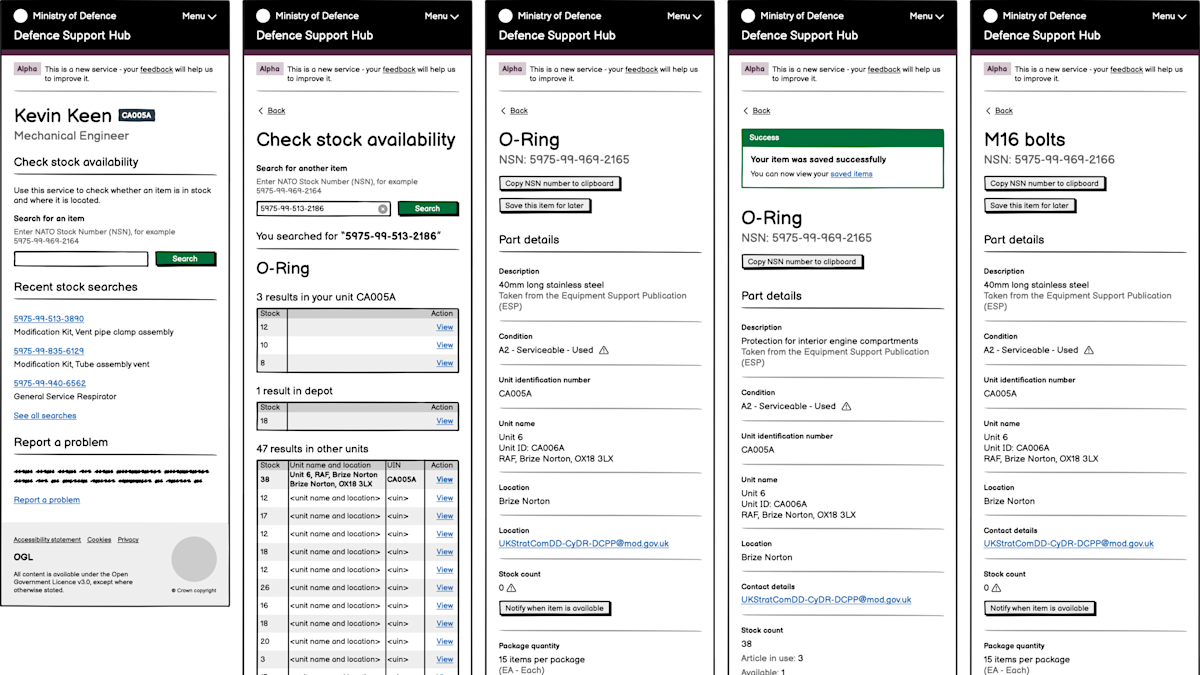
Check Stock Availability
This enables users to see stock levels and locations of the parts they need to complete their work.
As-is
- There was no self-serve route for users like mechanical engineers to be able to see stock availability data
- They are dependent on getting the information manually from logisticians
- Logisticians are commonly a single point of contact for multiple engineers
Our research activities
- Online survey with 262 respondents across various ranks and roles
- 4 site visits with 20 users (Delhi, Keogh, Mons and Dalton Barracks)
- In-depth user interviews
- Low-fidelity prototype testing remote and in-person with targeted users
Our research showed that this service would deliver significant value to various user groups. It confirms the need for engineers to have direct and easy access to stock availability information.
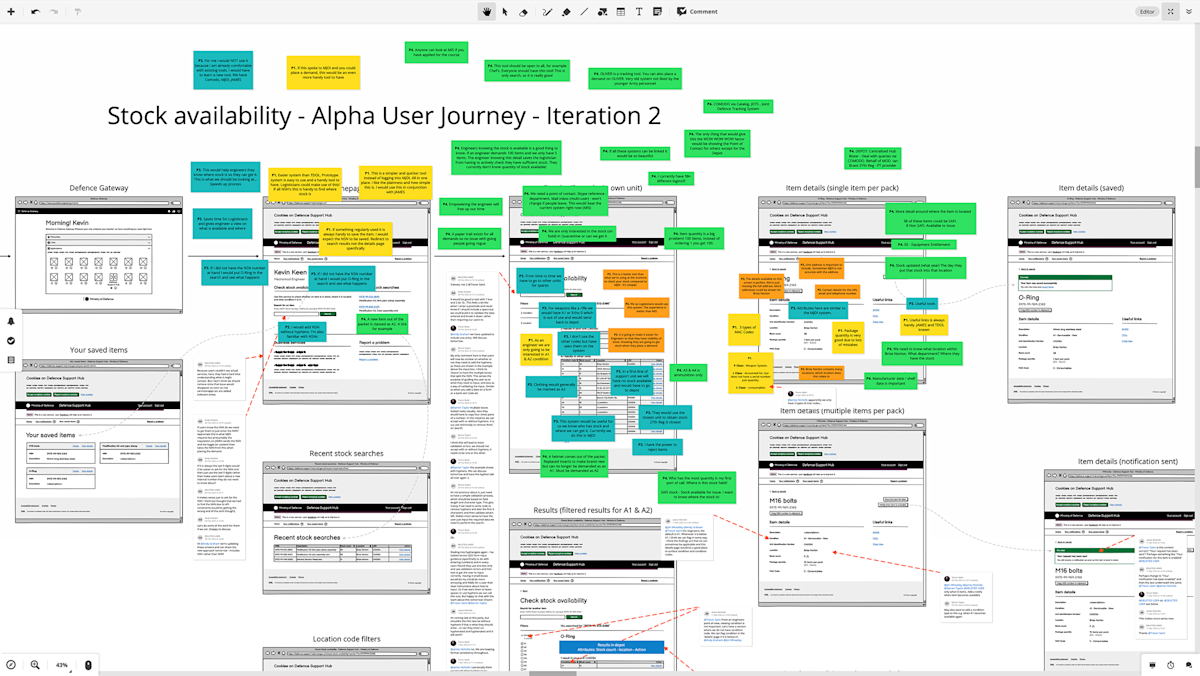
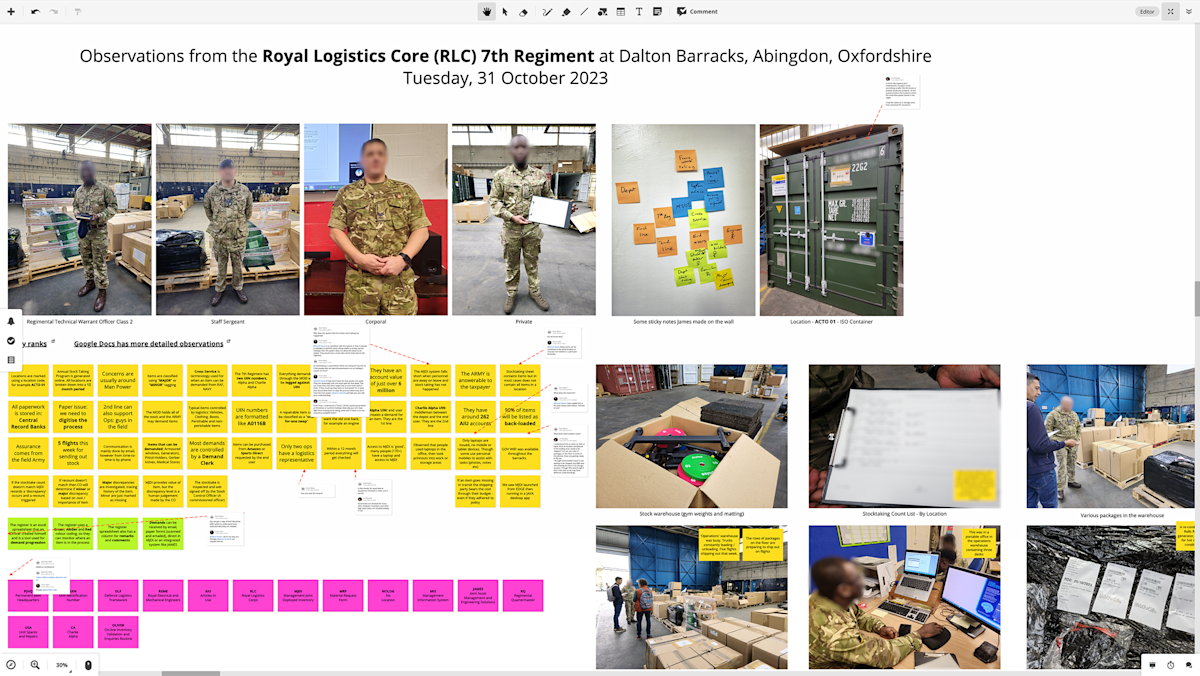
Our key findings
Although our main users were mechanical engineers, we found that logisticians were also very interested in the service because it gave them faster and easier access to information about the Management of the Joint Deployed Inventory (MJDI).
We also discovered that other groups, like armourers and military transport personnel, had similar needs to mechanical engineers, widening the potential user base for the Check Stock Availability service.
Our paper prototypes performed very well in real-world tests, with users reporting high satisfaction. We gained valuable insights into user experience and information needs, which will guide future improvements. Much of our research, including usability testing, has shaped the latest version of the prototype.
Army personnel on the shop floor
We met with various army engineers and logisticians on the shop floor, who walked us through the process of ordering spare parts and general logistics.
Fig. 1 - Army Sergeant Fig. 2 - Army Lance Corporal Fig. 3 - Army Warrant Officer Class 2 (WO2) Fig. 4 - Army Private Fig. 5 - Storage ISO container Fig. 6 - Army Land Rover being worked on by Engineers
Research videos
During our research visits, we captured video recordings of all our discussions and how army personnel engaged with our prototypes. These recordings allowed us to share insights with the team and identify opportunities for further improvements.
Additionally, we compiled key highlights from the research footage to present to our stakeholders. This helped illustrate the challenges faced and demonstrated how our system could effectively address those pain points.
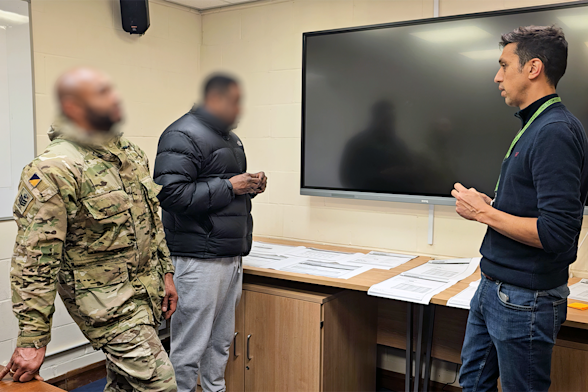
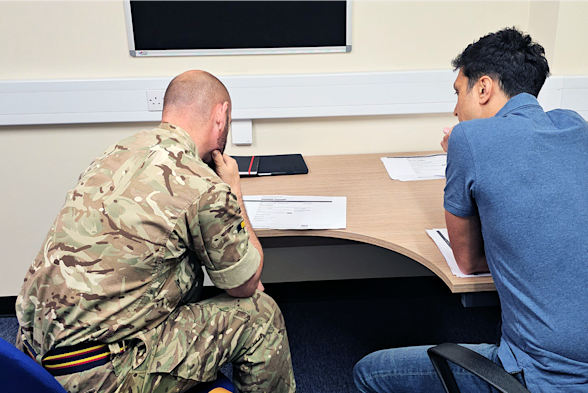
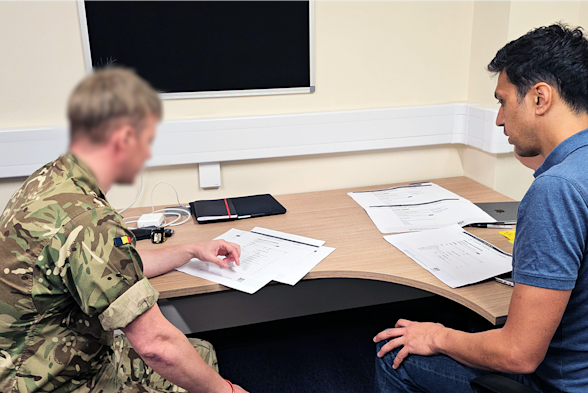
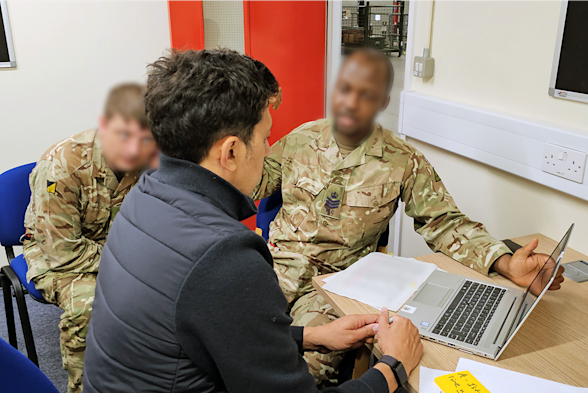
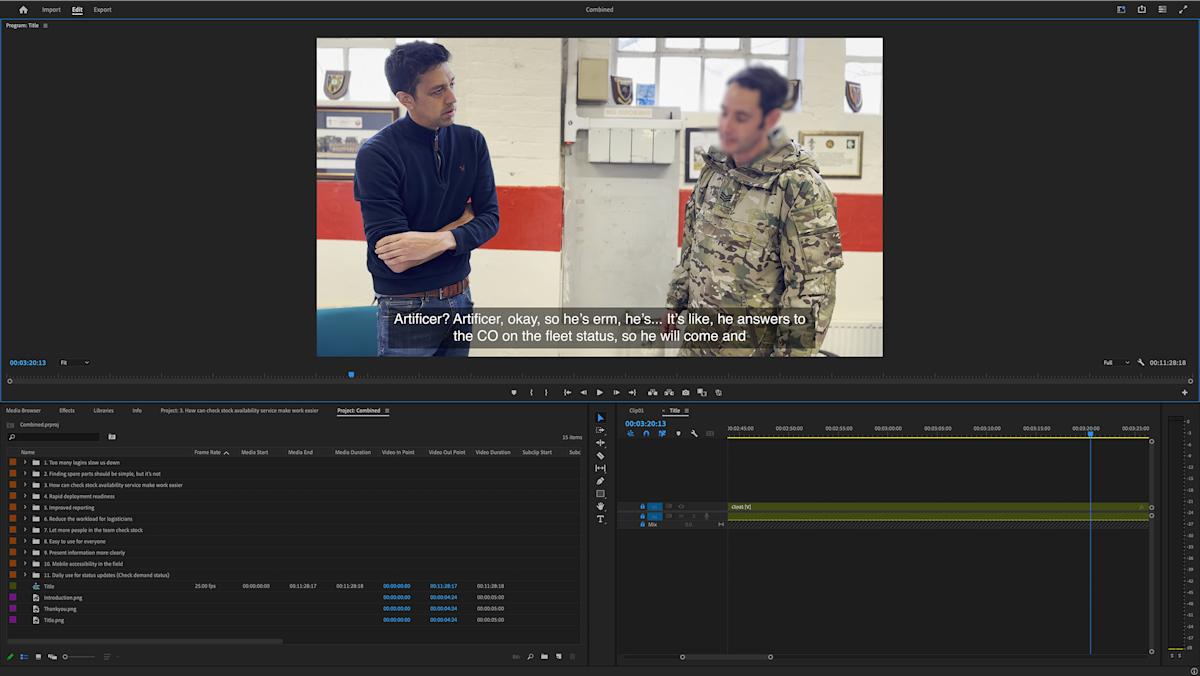
Our survey results
The survey results confirmed what we had learnt during the discovery phase and backed up our insights from the Alpha Phase:
- 79% of engineers rely on logisticians to check stock availability, which can cause delays, miscommunications, backlogs, and more work for the logisticians
- 46% of engineers are unhappy with the current ways of checking stock availability
- 87% of engineers surveyed are interested in checking stock availability themselves
- 78% of respondents said that having direct access to stock information is very important
We tested both paper prototypes and digital wireframes that allowed users to check stock availability on their own. The feedback was very positive, suggesting this could lead to major improvements in operations.
High fidelity design
High-fidelity designs for the entire end-to-end journey were developed in Figma, based on the variations we had initially sketched in Balsamiq, which tested successfully. We ensured that the designs were created for all screen resolutions, with interactions thoughtfully adapted to suit different screen sizes.
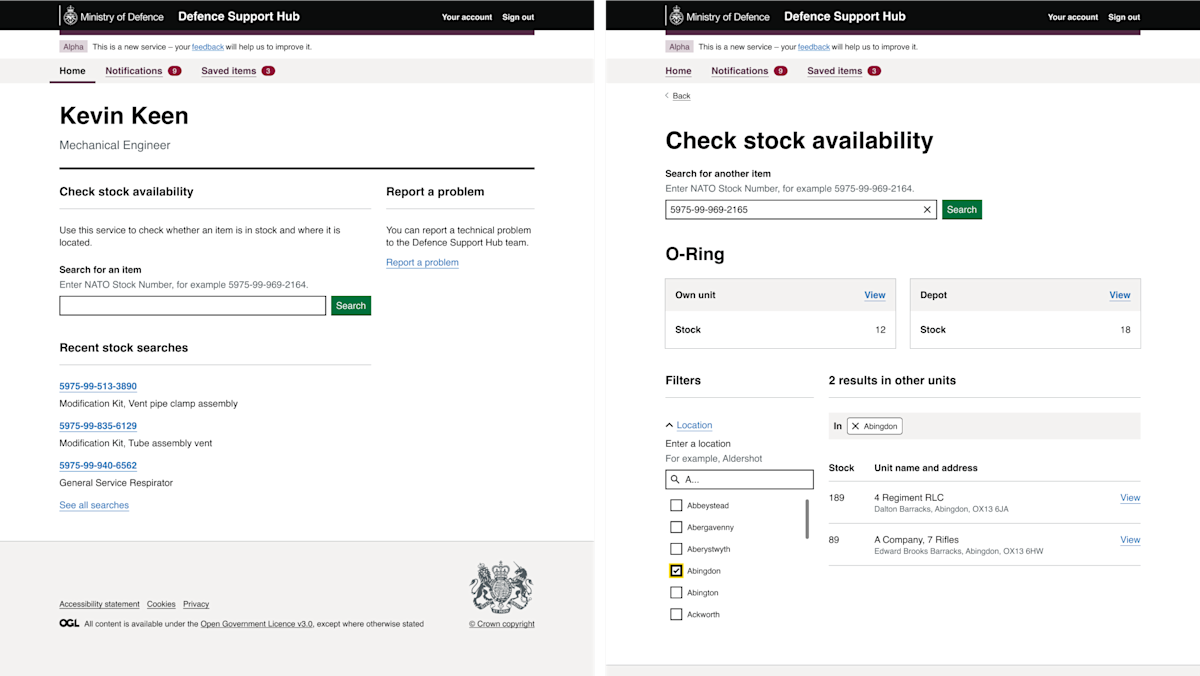
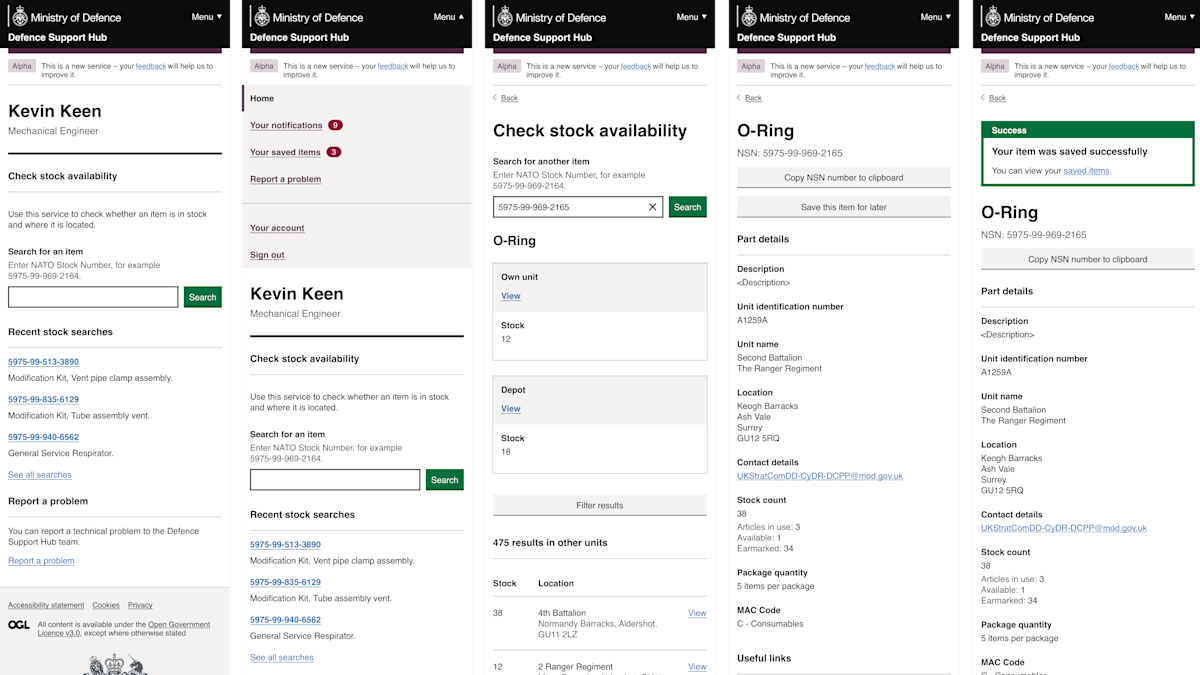
Prototyping design into code
Later, we moved designs into prototype code. This allowed us to provide an interactive and more realistic user experience over flat design which was more representative of a real service.
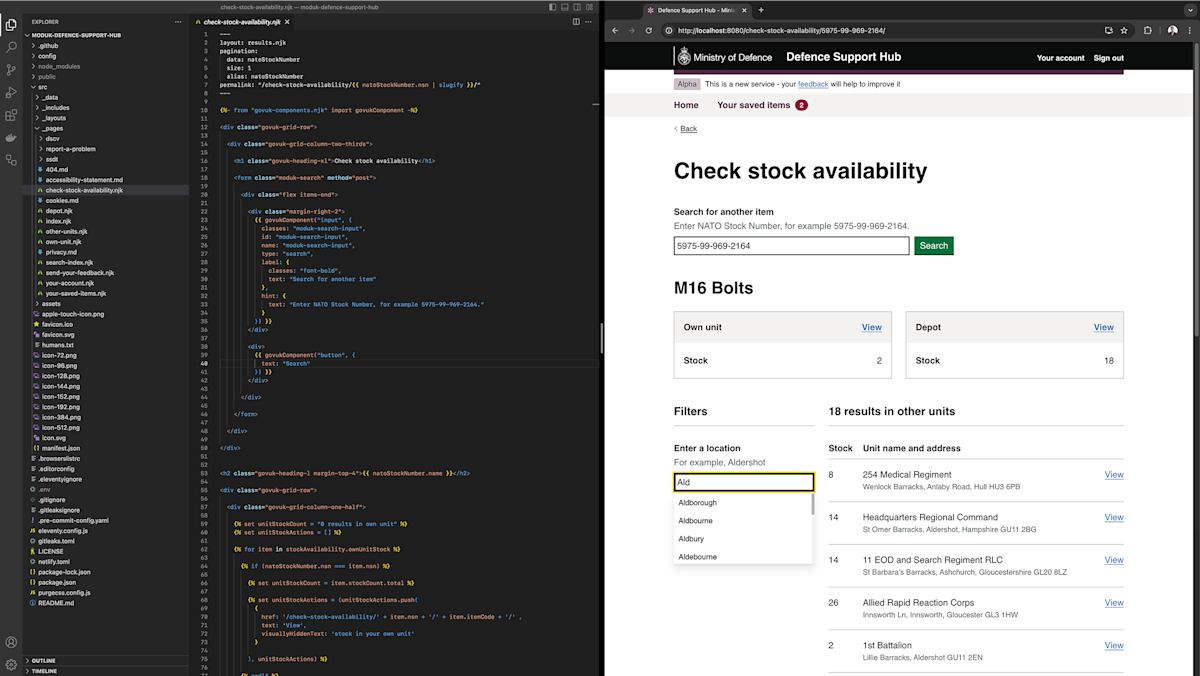
The results
We successfully completed the discovery and alpha phases of a highly complex end-to-end digital service, enabling engineers and logisticians to check stock levels across various locations. This was accomplished through extensive user research and multiple design iterations.